Automation and robotics in Zalando's European logistics network
Automation and robotics in Zalando's European logistics network
How mobile robots, artificial intelligence and automation technology support employees in unergonomic and monotonous areas.
How mobile robots, artificial intelligence and automation technology support employees in unergonomic and monotonous areas.
Zalando continuously invests in the automation of work processes in logistics, both to make the work of employees easier and to provide customers with first-class service. Automation, artificial intelligence and robots are already in daily use at Zalando to support logistics employees - and help to process customers' orders even more efficiently.
TORU - from 28 robots to 57
The mobile robots are called TORU, were developed by the robotics company Magazino and have been in use in Zalando logistics since 2018. The robots - designed to relieve logistics employees of unergonomic tasks - reach for individual shoe boxes, pick them up and transport them to the appropriate storage area. The robots not only work in the picking racks, where space is at a premium, but can also pick up and transport products individually.
Following a successful test phase at the Erfurt logistics center, 16 TORU robots are now in operation at the site in Lahr/Black Forest. Here they transport up to 6,000 shoe boxes per day.
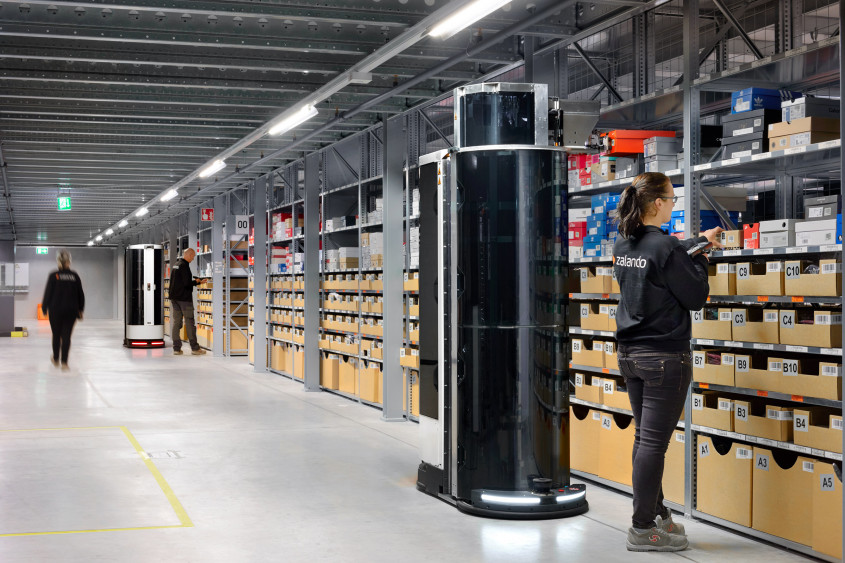
Marcus Daute, Director Logistics Product & Strategy, says: "We are constantly on the lookout for new smart technologies, especially for work that is often repetitive. The robots support our employees in less ergonomic and monotonous tasks in shoebox picking. Since the concept has proven successful in our logistics center in southern Germany, the TORU robot fleet will relieve colleagues at two other locations so that we can continue to offer our customers a very good service."
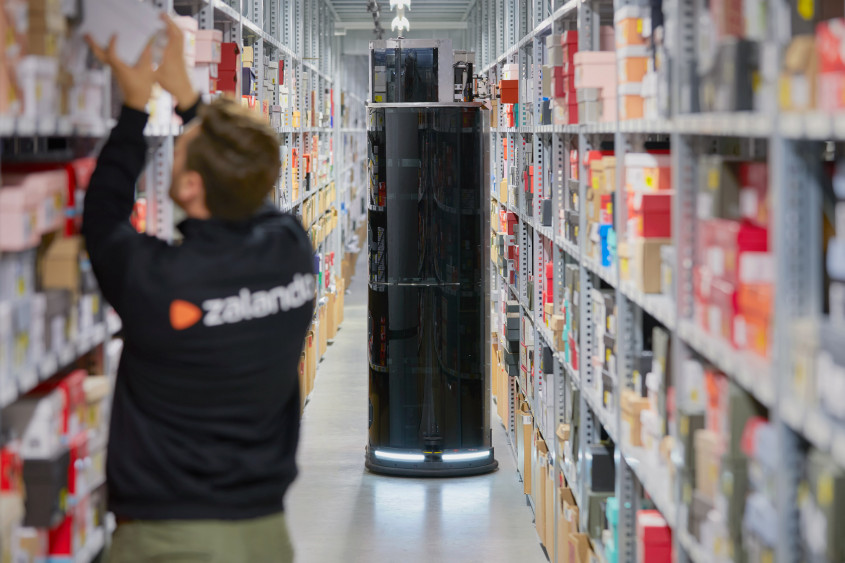
The technology still reaches its limits in some places when it comes to spontaneous changes in the process flow. Marcus Daute says: "The know-how of our colleagues in logistics is indispensable for the success of automation. The TORU robots can only help if they receive support. We have observed, for example, that the robots are less able to deal with inaccuracies within a picking rack. For example, they need a precise arrangement of shoe boxes. This attention to detail can be guaranteed by our employees, who store the shoe boxes very precisely. So, we work hand in hand with new technologies to achieve the best result for our customers."
Driverless through the logistics center
To further improve workflows for logistics employees, Zalando also uses autonomous mobile robots for automation. The robots - provided by idealworks, a subsidiary of the BMW Group - support Zalando's employees with autonomous transfers that require little supervision. At Zalando, they are used for internal transfers of empty cardboard boxes and packaged orders between two sorting machines in the shipping area. The robots can travel at speeds of up to 8 km/h on a 50-meter route. They receive their transport orders via idealworks' fleet management software, which is connected to Zalando's central IT system, ZalOs. After a successful test phase at the logistics center in Mönchengladbach, where we currently have three mobile robots, the fleet has now been expanded by additional four robots in our site in Lahr/Black Forest.
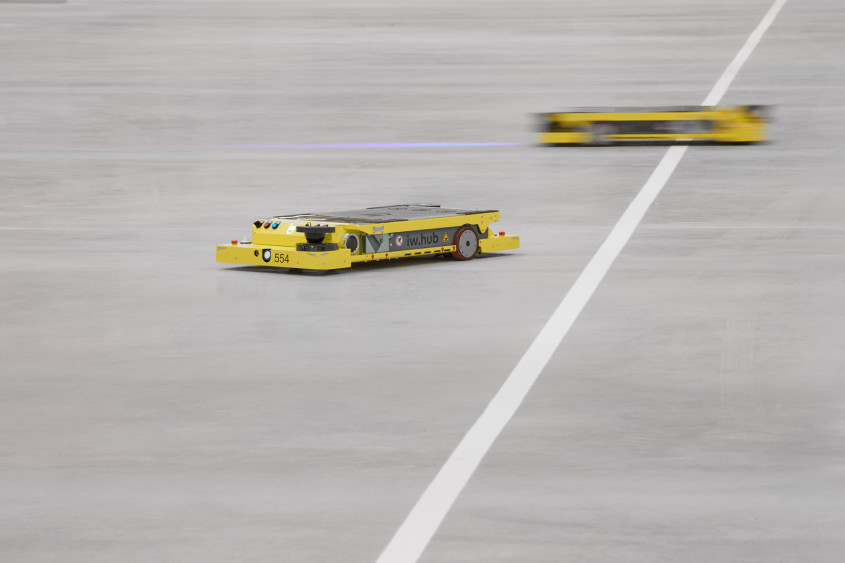
Marcus Daute says: "The transport route of the robots may seem comparatively short. However, the journeys take place very frequently and run autonomously; this has a positive effect on the distribution of tasks among our logistics colleagues. In the past, they transported the packages themselves in logistics carts. That was a monotonous task that is now being taken over by a machine. Our colleagues can now concentrate on more demanding planning activities, such as loading parcels into trucks."
Artificial intelligence controls flow of goods
We not only use automation technology in logistics, but also in intelligent algorithms. Artificial intelligence helps us to optimize our logistics processes, for example to reduce lead times and calculate optimized delivery routes to fulfill an order. One example of this is our specially developed merchandise management system, which controls flows of goods and processes for handling orders. As a result, we are always able to adapt our processes quickly and flexibly. Among other things, this system helps us to derive data from the past so that we can plan our customers' ordering behavior, e.g. for peak periods such as Cyber Week.
The automation of manual sorting
We are convinced that humans and automation complement each other very well. We use technologies that, on the one hand, take over physically demanding or monotonous tasks from our employees. On the other hand, technologies increase service to our customers. For example, various types of sorters are used in our logistics centers. The so-called pocket sorter is a mobile warehouse within the new generation of our logistics centers and enables simplified storage and retrieval of particularly popular items. In the so-called line sorter, employees place individual products in mechanically connected trays. A pusher then automatically transports the items to specific chutes, where all the items in an order are brought together. The outbound sorter automatically sorts the finished packages via several chutes to the various destinations with different shipping possibilities.